How Injection Mold Gate Systems Work
Today, we're diving into the world of injection mold gate systems. If you've ever wondered how these crucial components can make or break your molding process, you're in the right place. Let's explore the ins and outs of gate systems and discover how choosing the right one can elevate your production game.
When it comes to injection molding, the gate system serves as the entry point for molten plastic to flow into the mold cavity. Think of it as the gateway that determines how smoothly and efficiently the material fills the mold. Selecting the right gate system is key to achieving high-quality, consistent parts.
The Different Types of Injection Mold Gate Systems
Sprue Gate
The sprue gate is the most common type of gate system, connecting the runner to the mold cavity directly. It's effective for single-cavity molds and offers easy gating control. However, it can result in visible gate marks on the part and may require additional trimming.
Edge Gate
An edge gate is located at the edge of the part, allowing for easy removal and reducing the need for post-processing. It's suitable for thin-walled parts but may cause aesthetic issues due to gate vestige.
Sub Gate
Sub gates are situated beneath the part and are ideal for gating on the part's non-visible surface. They help minimize gate marks on the finished product but can be challenging to remove and may require additional design considerations.
Hot Runner System
The hot runner system keeps the material in a molten state within the runner, leading to reduced cycle times and material waste. It's excellent for high-volume production but comes with a higher initial cost and maintenance requirements.
Factors to Consider When Choosing an Injection Mold Gate System
The type of material being used for injection molding plays a significant role in gate system selection. Different materials have unique flow characteristics that can impact gating design and performance.
Part Design and Geometry
The design and geometry of the part will influence the gate location and size. Complex parts may require multiple gates or specific gating configurations to ensure proper material flow and part quality.
Production Volume and Cycle Time Requirements
Consider the production volume and required cycle times when choosing a gate system. Some systems, like hot runners, can significantly reduce cycle times, while others may be more cost-effective for low-volume production runs.
Cost Considerations
While hot runner systems offer efficiency benefits, they also come with a higher initial cost. Evaluate your budget and long-term production goals to determine the most cost-effective gate system for your needs.
Benefits of Using an Efficient Injection Mold Gate System
Choosing the right gate system can result in better part quality and consistency. Proper gating helps avoid defects such as sink marks, warping, and short shots, leading to higher overall product quality.
Reduced Cycle Times and Production Costs
An efficient gate system can streamline the molding process, reducing cycle times and production costs. Faster fill times and minimized material waste contribute to increased efficiency and cost savings.
Minimized Material Waste
By optimizing the gate system, you can minimize material waste during the injection molding process. Proper gating ensures that the material flows evenly and completely into the mold cavity, reducing scrap and rework.
Enhanced Overall Efficiency and Productivity
Maximizing the efficiency of your gate system translates to enhanced overall productivity. With faster production cycles, improved part quality, and reduced downtime, your injection molding operation can operate smoothly and efficiently.
Conclusion
Choosing the right injection mold gate system is crucial for achieving optimal results in your molding process. By considering factors such as material selection, part design, production volume, and cost, you can select a gate system that maximizes efficiency and quality. So, take the time to evaluate your options and find the perfect gateway to producing perfect parts!
We specialize in precision injection mold making and plastic molding processes for 20 years, contact yoyo@hanking-mould.com for your plastic mould projects.
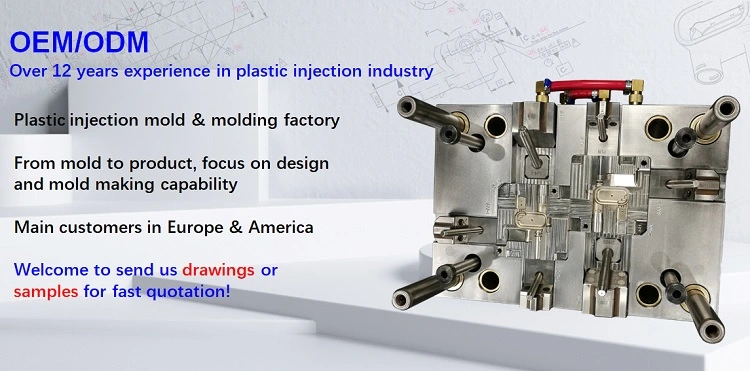